Success through innovation
2001: Building Services Award for developing the MIRA low-energy oil-fired boiler with Perpetum burner.
2003: For the PMX pellet boiler
2004: For fully automated pellet feed
2005: For the BioWIN pellet boiler
2006: For the FireWIN pellet boiler (Federal Ministry for the Environment, Austria)
2006: For the FireWIN residential pellet boiler
2008: International environmental symbol for the BioWIN and FireWIN pellet boilers
2009: For the pellet boilers for BioWIN and FireWIN
2010: Nomination of the VarioWIN pellet boiler
2015: For the DuoWIN hybrid boiler (Federal Ministry for the Environment and the Province of Upper Austria)
2016: For the PuroWIN wood chip boiler (fire category)
2016: 2nd place in the "Innovation" category for the PuroWIN wood chip boiler
2016: For innovation, high quality, functionality and ecology for the PuroWIN wood chip boiler
2016: For the PuroWIN wood chip boiler
2017: For the PuroWIN wood chip boiler (Federal Ministry for the Environment and the Province of Upper Austria)
Certified Climate Alliance company
Windhager uses energy saving potential
Windhager has been a certified Climate Alliance company since 2007. In our daily work, in all areas of the company, we take care to act in way that protects the climate and the environment. Various measures have already been successfully implemented for years, including:
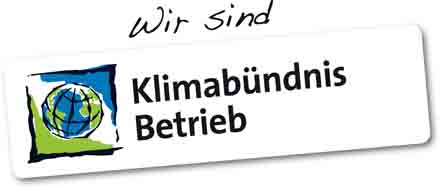
- Mobility concept: Employees are picked up and brought home on the company’s own buses.
- Energy accounting: Precise monthly records of electricity and fuel consumption are kept in order to quickly identify potential savings.
- Waste heat utilisation: Waste heat from production is fed directly into the heating system, and compressor waste heat is used in the drying chamber.
- Automatic lighting control: In many production areas, lighting systems are turned off via a timer during breaks.